Hongfa has 80 AAC plant (Autoclaved aerated concrete) for domestic and abroad market. Main raw materials of AAC are siliceous material (sand, fly ash and Silicon tailings) and Calcium materials (lime and cement) mixed with foaming agent (aluminum powder). It is the product of light porous silicate through the following processes: batching, mixing, pouring, hardening, cutting, autoclaving and curing etc. Because of large amount of well-distributed tiny pores after foaming, it is named autoclaved aerated concrete.
Project Proposal of AAC block plant, the annual output ranges from 50,000 to 300,000m³.
AAC block history and features
- Autoclaved Aerated Concrete block is one kind of environmental block.
- In fact AAC was perfected in the mid-1920s by the Swedish architect and inventor Dr. Johan Axel Eriksson, working with Professor Henrik Kreuger at the Royal Institute of Technology.
- Since it went into production in Sweden in 1929 in a factory in Hallabrottet and quickly became very popular.
- In the 1940s, the trademark Ytong was introduced, and was also often referred to as "blue concrete" in Sweden due to its blueish tinge.
- It used siliceous (fly ash, sand, slag) and calcareous (lime & cement) as the main raw materials, which through the process of batching, pouring, pre-curing, cutting, autoclaving, separating and packing to make into the final products.
- AAC block can be made into many kinds of bricks(for example:600×200×100,80×80×180,240×115×53,600×200×125),they could be used industry building and common building. AAC Block is the most mature technology of production and application in the worldwide nowadays.
- The product has light weight, high compressive strength, excellent thermal insulation, great acoustic insulation and high fire resistance.
- AAC has a large variety of sizes, and it is easy for nailing and milling like wood. So it is perfectly workable product.
- Raw materials include cement, lime, fly ash, gangue, river sand and aluminium powder etc. Production through batching, mixing, casting, cutting and autoclaving.
AAC Classification
In general, it can be classified according to the types of raw materials, manufacture process and functions.
Based on the shape of AAC products, it can be divided into AAC block and AAC panel. It is a revolutionary material offering anunique combination of high durability and strength, low weight, excellent heat insulation, fire resistant, noise absorption, unprecedented build ability and superior ecological green features. In China, AAC is one of the light wall materials which was popularized and applied at the earliest and the most widely.
Main Technical Specifications of AAC Block and AAC Plant
Annual Capacity (300 days) | Power | Daily Capacity | Cycle Time | No. of Autoclaves |
50,000m3/year | 400 KW | 166 m3/day | 10 hours | 2 |
100,000m3/year | 500 KW | 333 m3/day | 10 hours | 4 |
150,000m3/year | 630 KW | 500 m3/day | 10 hours | 6 |
200,000m3/year | 720 KW | 666 m3/day | 10 hours | 8 |
300,000m3/year | 900KW | 1000 m3/day | 10 hours | 10 |
Main Technical Specifications of AAC block
Volume density level
|
B06
|
B05
|
B04
|
|
desiccated density(kg/m³)
|
≤625
|
≤525
|
≤425
|
|
Strength level
|
A5.0
|
A3.5
|
A2.0
|
|
Drying shrinkage date
|
0.5
|
0.4
|
0.4
|
|
Freezing resistance
|
quality loss %
|
≤5.0
|
≤4.0
|
≤3.0
|
Strength after freezing(Mpa)
|
≥4.0
|
≥2.8
|
≥0.6
|
|
Dry coefficient of thermal conductivity [W/(m•k)]
|
≤0.16
|
≤0.14
|
≤0.12
|
Working process
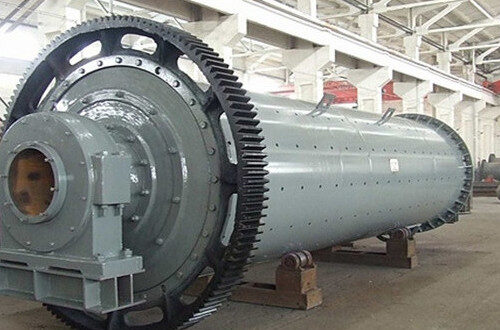
Sand&Lime Milling

Batching, Mixing, and Pouring Process

Aerated Autoclaved Process
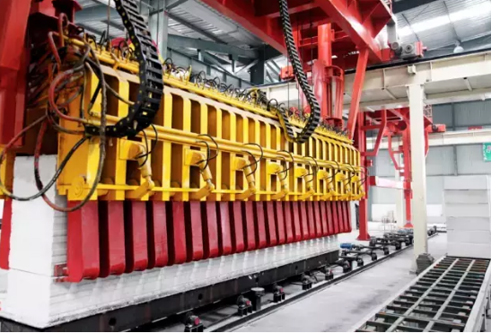
Finished Block Dealing Process
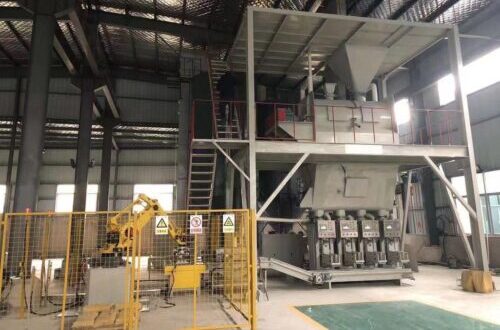
Weighing System

Curing Process

Cutting Process

Packing Process
AAC panels with steel mesh cages or steel mesh sheets treated with anti-rust coating in the production of autoclaved aerated concrete blocks are available, max. length is 6m. Please contact us for a customized proposal.
Contact us
If you are interested in these products, please leave your message, our relevant staff will contact you quickly.